BRAND STORY 02
1931-1960
Solid Progress and Rebuilding from the Ashes.
Becoming an All-Around Manufacturer of Compressors and Coating Machines and Systems
The Tsunashima Factory, newly built in the 1950s
The Shadow of War Looms Over the Company’s Growth
Spurred on by its acclaimed products, the company builds a second factory, but everything is reduced to ashes following two air raids.
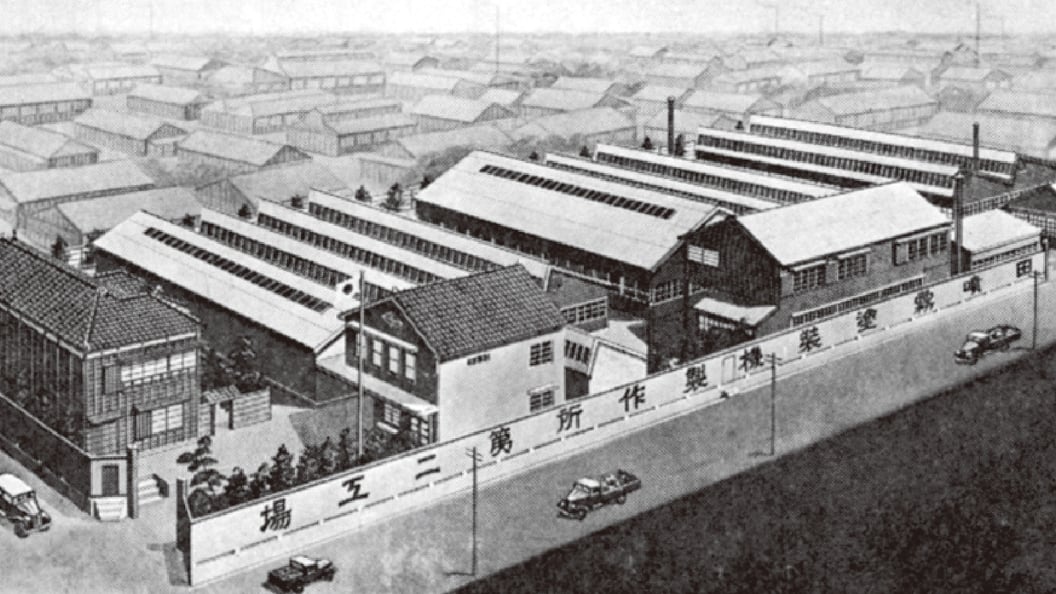
With its spray guns and air compressors garnering acclaim for their excellent performance, the company continued to ramp up production to meet market demand. In 1936, it leased land of about 500 tsubo (1 tsubo being roughly equal to 3.3 square meters) in Shimo-Maruko, Ohta Ward, on which it built a second factory. By June 1940, all production facilities had been moved to Shimo-Maruko, leaving only the headquarters’ sales office in Ebisu, where the first factory had been. Also, as the company was incorporated as a limited partnership, its name was changed to Iwata Spray Coating Equipment Seisakusho, Ltd. While the company was enjoying steady growth, however, the shadows of war began to loom over its activities. The year 1937 saw the promulgation of the Act on Temporary Measures on Imported and Exported Goods, etc., the Temporary Fund Adjustment Act, and other laws intended to give priority to the military industry. The National General Mobilization Act, which was proclaimed in April 1938, made it difficult for the company to procure materials or secure manpower. With all kinds of materials now rationed, Iwata Seisakusho experienced a noticeable decline in production from 1939 to 1940, as its stock of materials was depleted. Starting from the end of 1944, employees of the company dug the ground behind Gumyoji Station on the Keihin Kyuko Line, and built an underground factory there. But, just as they were about to move the equipment to this makeshift factory, two air raids took place on March 9 and April 15, 1945, and burned down the Shimo-Maruko Factory, reducing the manufacturing facilities and the food stockpiled for employees to ashes. Leaving them powerless to do anything more, the war ended on August 15, 1945.
Rebuilding the Company Out of the Ashes with 18 Employees
The company starts to rebuild by making household milling machines and agricultural sprayers. Eventually, the number of inquiries regarding coating equipment rises, and it returns to its main business.
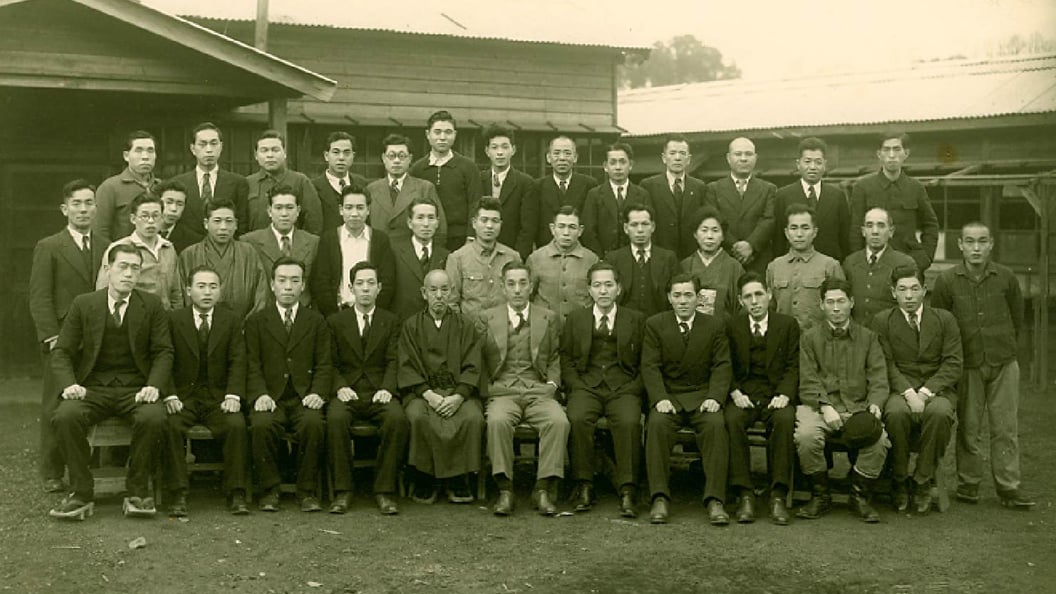
After the war ended, Japan faced unprecedented predicaments such as food shortages, and Iwata Seisakusho was no exception. In order to support the livelihoods of its employees, the company needed to dig its way out from the ashes. On September 27, 1945, a total of 18 employees gathered and embarked on the task of rebuilding the company. They started with everyone going out to collect scrap materials, and constructing a shack next to the underground factory. Then, they pulled out what machines and tools were left from the ashes, and repaired them to assemble what could barely be called a production system. For the time being, they decided to manufacture items that were essential to people's everyday lives, instead of air compressors and spray guns. It was around the middle of 1947, when the dust of postwar confusion began to settle, that Iwata Seisakusho started to receive orders again for coating equipment sporadically. The opportunity for the company to return to its main line of business had come earlier than expected.
Expanding the Factory and Developing New Products
The company redesigns its spray guns using its own technology. It expands its compressor production facilities, anticipating the trends of the time.
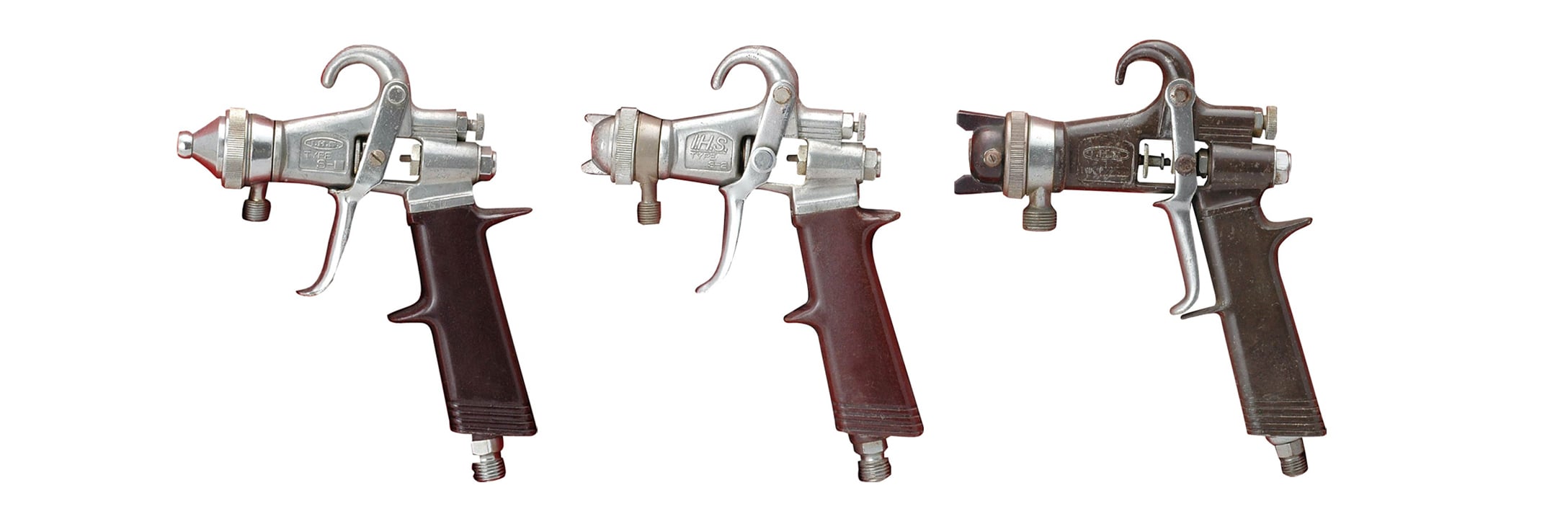
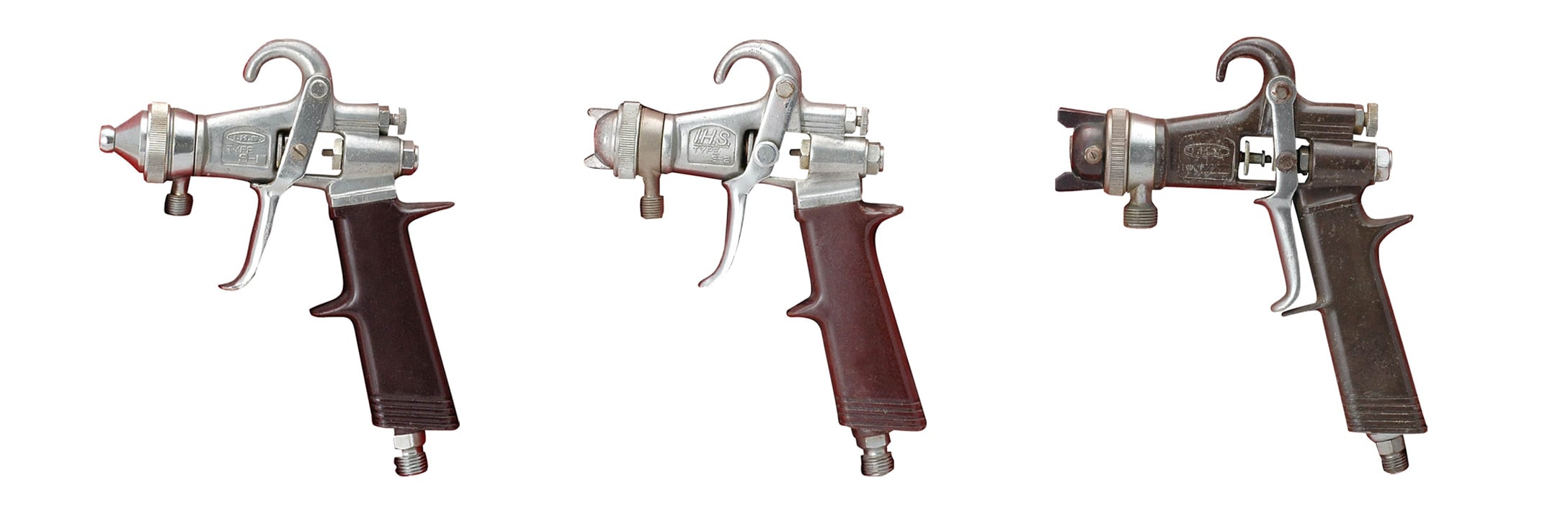
In September 1948, Iwata Seisakusho increased its capital by 302,000 yen, bringing its capital to 500,000 yen, and embarked on constructing new factories and developing new products. The primary focus was on the overall redesign of spray guns. As the company was making a fresh start after the war, it decided to develop new spray guns using its own technology. It came up with two spray gun models, type S and type B. The most remarkable feature of these guns was that they needed only a small amount of air to function. Their exterior designs were also entirely new. The type B gun became popular for its large spray volume, which made work more efficient. The type S gun featured an easy grip sized to fit the hand of the average Japanese worker, and was cost-efficient, since it could be used with a low-output compressor. On the other hand, air compressors require more sophisticated manufacturing equipment than that used for spray guns, and it was difficult for the company to ramp up their production with only the war-battered machines and tools on hand. Therefore, in September 1949, the company took out a bank loan and bought used lathes, turret machines, grinders, and other equipment from major heavy industry firms. And by borrowing more money with the machinery as collateral, the company rapidly expanded and upgraded its production facilities. Up until then, it had taken a cautious approach regarding business, opting to do all business activities with their own cash reserves. This represented a bold departure, a decision the company made based on its reading of the trends of the time.
Responding to the Increase in Production as the Japanese Economy Gets Back on Its Feet
The company builds a new factory in Yokohama to meet demand, and announces the establishment and IPO of Iwata Air Compressor Manufacturing, Co., Ltd.
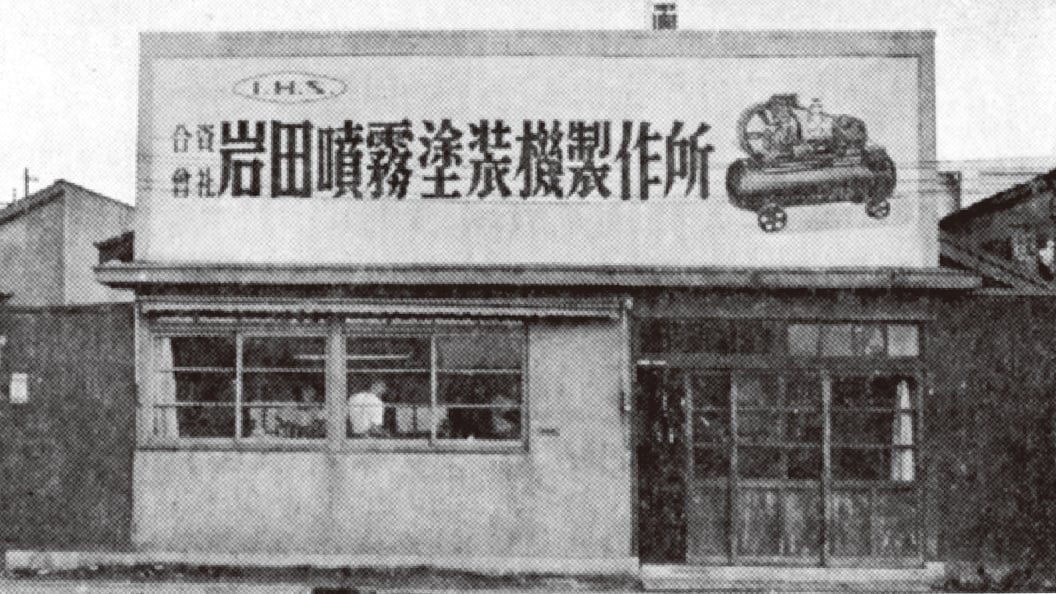
The Japanese economy roared back to life, thanks to the special procurement boom that took place after an upheaval broke out in 1950. As the company ramped up production, it became necessary to review and revamp its overall management structure. The first item on the agenda was the production facilities. The factory in Gumyoji had been expanded time and again to meet the growing demand, but even those extensions were reaching full capacity. The company decided to build a new factory in Minami-Tsunashima, Kohoku Ward, Yokohama, and moved all of the existing factory’s facilities to the new site by April 1953. They also decided to rebuild the shack-style headquarters in Ebisu following the completion of the new factory. Its construction was completed in 1956. In April 1957, Iwata Air Compressor Manufacturing Co., Ltd. was established, taking over the entire business of the limited partnership firm. This new company went public in 1961. In October 1956, the IHS Association was formed by 46 subcontractors with which Iwata Air Compressor Manufacturing had particularly close relationships. Company representatives attended the meetings that were held four times a year to explain their business policy and to exchange opinions, in an effort to keep the channels of communication open.
Anticipating Rapid Economic Growth and Developing into an All-Around Manufacturer
The company develops the WIDER 57 (W-57) spray gun over four years and regains the market share for automotive painting.
Around 1955, when the Economic White Paper proclaimed that the Japanese economy “could no longer be termed postwar,” industrial production in Japan started to grow exponentially. It heralded the beginning of the era of rapid economic growth. Iwata Air Compressor Manufacturing, which was gradually shifting toward a modern production system and management structure from around that time, was looking to ride this great wave. The biggest challenge it faced was in developing new products. In 1954, the company successfully developed rotary automatic coating equipment, which would become the prototype of the automatic coating equipment produced today. It also developed a flow coater, which is a machine that directs a stream of paint in the form of a thin, film-like curtain and coats the workpiece as it is carried under the stream. Thanks to these products, Iwata Air Compressor Manufacturing was able to develop new areas of business, and transformed itself into an all-around manufacturer producing air compressors, coating machines, and coating systems. Improvements were also made to the company’s main products, spray guns and air compressors. While manufacturers in the advanced nations of Europe and the US were developing spray guns according to rules of thumb, our engineers thought it would be possible to develop better spray guns by gaining a more thorough theoretical understanding of the mechanism. They spent four years thoroughly researching the relationship between the diameter of the fluid nozzle, the shape and size of the nozzle tip, and the atomization of paint. The results revealed that the degree of atomization was determined by the amount of air passing through the air hole, the central diameter of the air cap, and the amount of paint sprayed. The spray gun that was developed based on these findings was the WIDER 57 (W-57) model, introduced in 1956. The W-57 became hugely popular for its outstanding performance, and it wrested market share away from foreign-made products that had dominated the automotive painting market.
The company reduces the cost and improves the performance of small-sized compressors, and reinforces its sales network by placing sales engineers nationwide.
In the air compressor market, demand was growing for inexpensive, easy-to-maintain products with high compression efficiency. The company's engineers focused on the development of small-sized air compressors, and making them rotate at higher speeds. After a considerable amount of trial and error, they succeeded in developing the C-O-10 and C-O-11 models in 1955. The air compressors of the C-O series were small in size, and reached rotational speeds of up to 900 rotations per minute (compared with 500 rotations per minute reached by previous models). In 1962, the company began to use standardized parts for cylinders, pistons, connecting rods, and other components, thereby enabling mass production, which in turn drove down prices. Furthermore, as technological expertise was poured into reducing vibration and noise, improving durability, and other aspects, small-sized air compressors came to account for more than 50% of the company’s overall sales. Alongside its efforts in product development, the company continued to streamline its production line to cut costs and boost production efficiency. The assembly line method was introduced for air compressors and other bestselling products, in order to bring down costs further. Another major challenge that the company faced in addition to developing new products was the reinforcement of its sales network. Around 1960, the company divided the country into ten blocs, established its own sales offices, and staffed these offices with sales engineers in order to increase its sales capabilities.
Augmenting Production Capacity After Several Spurts of Rapid Growth in Sales
The volume of orders starts to exceed production capacity, prompting the company to build a new compressor factory.
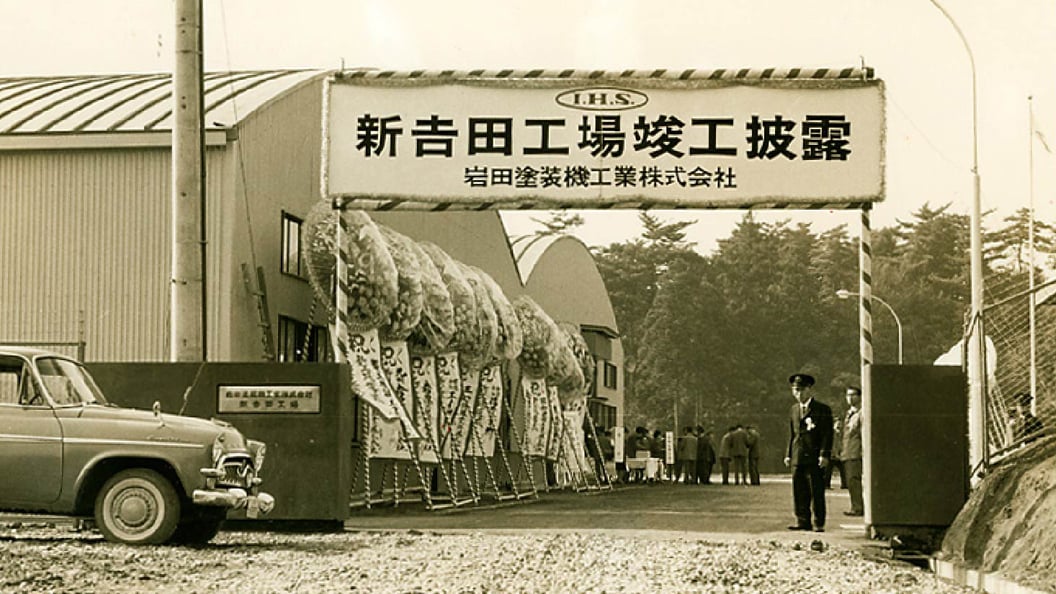
Iwata Air Compressor Manufacturing had managed to meet the growing demand by streamlining its production system, expanding the facilities at the Tsunashima Factory, and introducing a day-night shift system for some of the processes. However, from 1959 to 1968, the company experienced several sharp increases in sales, with the volume of orders ultimately exceeding production capacity. The company had been worried about such an eventuality, and had been considering expanding its factory facilities since 1961. After reviewing a number of proposed plans, it decided to build a new air compressor factory near the site of the Tsunashima Factory. A total of 170 employees were transferred to this new factory, named Shinyoshida Factory (No. 2 Factory, where our headquarters are currently located). It started operations in September 1962.